News & Events
Recycled magnets to reduce international dependence on rare earths and environmental impact
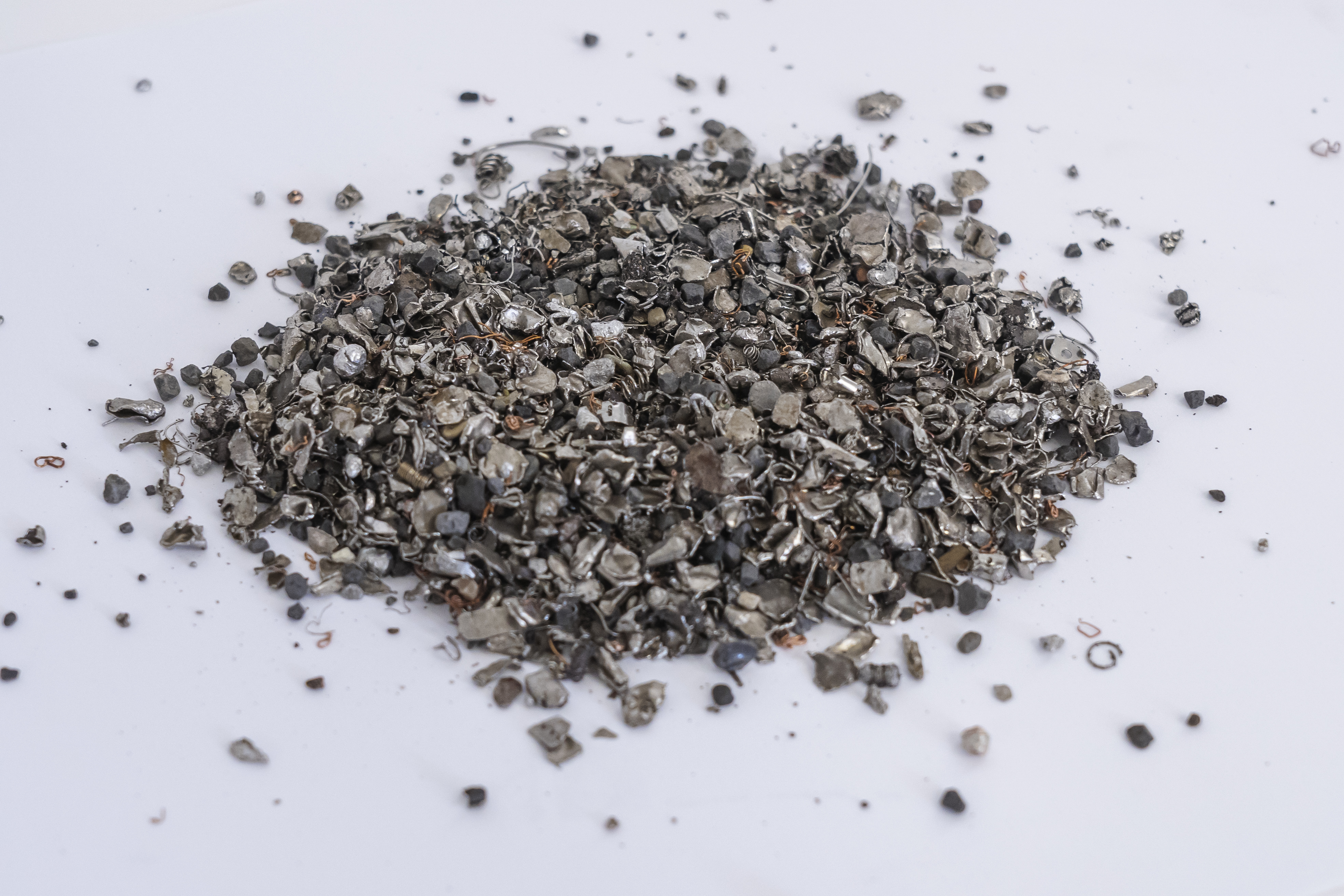
27 | 03 | 2023
The Cheapremag project has come to an end, in which the Ceit Technology Centre took part with a view to contributing towards the generation of an entire value chain within Europe, based on the recycling of rare earth magnets at the end of their useful life.
The project will enable international dependence and environmental impact to be reduced, as well as boosting the circular economy, while also allowing for less volatility in terms of prices and creating an alternative to the quasi-monopoly currently enjoyed by China, where most production of this raw material is concentrated.
Rare earths are considered by the EU to be an essential raw material, as stated in the classification of Critical Raw Materials. Having said this, most of its production from primary resources is concentrated in China, which is also the only country in the world that maintains a presence throughout the value chain – two factors that put the Asian country in a dominant position on the rare earth magnet market and enables it to impose its regulations. Specifically, Europe imports 16 thousand tons of rare earth magnets every year, which accounts for 98% of what it uses. All this puts both price control and supply to European companies in jeopardy.
Reduction in international dependence
The Cheapremag project was set in motion with a view to contributing towards the generation of an entire value chain within Europe based on the recycling of magnets at the end of their useful life. Cheapremag is funded by EIT Manufacturing and the Ceit Technology Centre took part in it, together with its project partners Fraunhofer IFAM, Mondragon Unibertsitatea, Copreci, and Magneti Ljubljana, who worked for a year researching into the recovery of magnets from electrical devices such as motors, generators and computers.
Rare earth magnets are manufactured via a powder metallurgical process, i.e. taken from the material in powdered form and then processed using a range of technologies such as compression moulding, injection moulding, compacting and sintering. As a technology centre considered an expert in this field, Ceit was on the one hand in charge of manufacturing the material in powdered form from magnets at the end of their useful life using a gas atomisation process and, on the other, collaborated in the manufacture of magnets on a laboratory scale via compression moulding.
A solution for multiple sectors
The solution developed by the consortium will be able to be used in multiple sectors, such as the car industry, industrial electronics, consumer electronics, robotics, aeronautics, medical instruments and measuring instruments, etc. Moreover, highly industrialised regions like the Basque Country are net importers of rare earth magnets, which means that the project enables an approach to be pursued towards the local or national generation of a recycling network that covers all the links in the value chain.
The Cheapremag project will enable international dependence (and, therefore, the risk to supply), environmental impact and the generation of residues and carbon emissions to be reduced, as well as boosting the circular economy and allowing for less volatility in terms of magnet prices via the very existence of an alternative to the quasi-monopoly enjoyed by China.